Производство легированных стальных отливок для энергомашиностроения
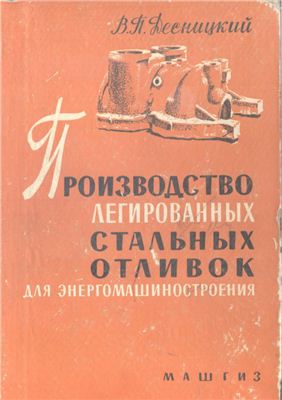
Десницкий В.П
Машгиз, 1961 г.
ОСОБЕННОСТИ ПЛАВКИ И РАЗЛИВКИ ЖАРОПРОЧНОЙ СТАЛИ, ВЫПЛАВЛЕННОЙ В ДУГОВЫХ ЭЛЕКТРОПЕЧАХ
Производство жаропрочной стали легче организовать на базе применения свежих исходных материалов. Особенно это касается выплавки сложнолегированных сталей, таких как ЛА1 и ЛАЗ. Выплавка стали в этом случае производится ступенчатым методом, первой стадией которого является сплавление свежих материалов в низоуглеродистую железоникелемолибденовую заготовку (ШЭП). Никель и молибден для лучшей дегазации присаживают до начала кипения металла, кипение проводят энергично, выжигая около 0,40% углерода.
Вторая стадия включает в себя выплавку стали заданной марки на шихте из ШЭП с коротким окислительным периодом и присадкой феррохрома в восстановительном периоде.
С А. Иодковским (ЦНИИТмаш) было произведено сопоставление нескольких методов плавки стали марки ЛА1 на свежих материалах плавки с кипением и восстановительным периодом под известковым шлаком; то же, но под шамотным шлаком; плавки методом сплавления с применением в завершающем периоде шамотного шлака. Наиболее эффективным признан последний метод, так как он дает возможность в весьма короткий срок значительно повысить температуру жидкого металла, получить сталь с низким содержанием кислорода, а также сократить продолжительность плавки, уменьшить расход электроэнергии и ферросплавов, идущих на раскисление металла. Пластические свойства при этом несколько повышаются.
Недостатками способа сплавления являются: опасность чрезмерного науглероживания металла; повышенный угар хрома, равный 5,1% по сравнению с 1,25 и 3,08 для первого и второго методов плавки; необходимость применения дорогой малоуглеродистой электропечной заготовки (ШЭП) с низким содержанием фосфора и серы, а также повышенное количество водорода из-за сокращенного периода кипения. В отношении последнего фактора С. А. Подковок я и приводит следующую зависимость (табл. 10).
Наибольшее количество азота в металле получается при плавке методом сплавления.
С выводами С. А. Иодковского о преимуществах метода сплавления можно согласиться лишь при условии работы электропечей на рядовых заправочных и огнеупорных материалах, что обусловливает необходимость максимального облегчения условий работы печной футеровки и сокращения в этих целях продолжительности плавки.
При хорошей стойкости подины, обеспечении высококачественным магнезитовым порошком марки МПМЗ и наличии хромомагнезнтового свода выплавка стали ЛА1 и ей подобных можете успехом проводиться с полным окислительным периодом без применения низкоуглеродистой никелемолибденовой заготовки. Количество окисляемого углерода должно быть в пределах 0.30—0,40%.
Однако выплавка стали на свежих материалах допустима только в начальный период освоения новых марок стали.
Типовой технологический процесс выплавки стали должен обязательно предусматривать использование отходов производства той же стали, содержащих дорогостоящие легирующие компоненты.
Наиболее распространенные жаропрочные стали аустенитного класса характеризуются, как правило, высоким содержанием хрома (13,0—27.0) и низким содержанием углерода (0.05— 0,20%). В тех случаях, когда содержание углерода ближе к верхнему пределу, можно использовать метод переплава (сплавления) отходов соответствующей марки и низкоуглеродистой шихтовой заготовки с добавлением в завалку недостающего количества никеля и ферросплавов. Корректировка состава присадками выполняется, как обычно, по результатам химического анализа первой пробы после расплавления.
Ввод титана и модифицирование (если оно предусмотрено) производится в конце плавки. Количество используемых в шихте отходов обычно находится в пределах 30—50%. Этот процесс наиболее рационален, когда в шихте имеется значительное количество ванадия и ниобия.
Метод сплавления неприемлем, когда надо получить в готовой стали содержание углерода ближе к нижнему пределу (менее 0,10%), и, кроме того, он затрудняет регулирование содержании углерода к моменту расплавления даже и при более высоком допустимом содержании.
Основные трудности переплавки высокохромовых отходов заключаются в изыскании таких методов обезуглероживания металла, которые не вызывали бы значительных потерь хрома в виде угара и в то же время не приводили бы к насыщению стали кремнием, применяемым для восстановления хрома.