Прочность термообрабатываемых прокатных валков
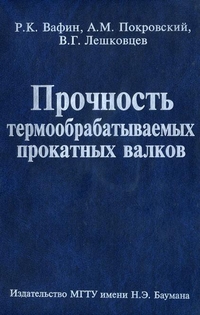
Вафин Р.К., Покровский A.M., Лешковцев В.Г.
МГТУ им. Н.Э. Баумана, 2004 г.
АНАЛИЗ ПРИЧИН ВЫХОДА ИЗ СТРОЯ ПРОКАТНЫХ ВАЛКОВ И МЕТОДЫ ИХ НЕРАЗРУШАЮЩЕГО И РАЗРУШАЮЩЕГО КОНТРОЛЯ
Стремление производителей повысить твердость бочки, которая, как известно [18], способствует увеличению износостойкости валков, приводит, во-первых, к охрупчиванию рабочего слоя, во-вторых, к формированию значительных остаточных напряжений. Последнее объясняется тем, что при закалке на большую твердость необходимо увеличивать скорость охлаждения валка с целью получения на поверхности бочки бейнитной или мартенитной структуры [4]. Более интенсивное протекание структурных превращений, связанных с изменением объема, и повышенные температурные градиенты при этом приводят к возникновению существенных термонапряжений.
Рассмотренная в 1.1 технология изготовления прокатных валков показывает, что в них после выплавки, разливки и ковки могут оставаться трещиноподобные дефекты металлургического характера. В присутствии растягивающих остаточных напряжений возможно страгивание и рост этих трещин, что может привести к разрушению еще на стадии термообработки, при хранении, тепловой посадке (для бандажированных валков), а также на начальном этапе эксплуатации [5, 21]. По естественному износу выходит из строя меньше половины рабочих и опорных валков. Оставшаяся часть приходит в негодность вследствие полного или частичного разрушения [18]. Все причины преждевременного разрушения прокатных валков можно разделить на три группы: конструктивные недоработки; нарушение технологии эксплуатации и недостатки изготовления [5].
К конструктивным недоработкам можно отнести неправильный выбор размеров бочки и шеек из расчета на прочность и жесткость валка при прокатке [14]. Так при эксплуатации опорных валков диаметром 1400 мм из стали 9X2 и 9ХФ на широкополосном стане 2500 горячей прокатки ММК [5] наблюдалось их массовое разрушение (80 %). Причиной выхода из строя валков, нормализованных до твердости 35-40 HSD, являлся, как выяснилось, недостаточный 1,5-кратный запас прочности. При увеличении диаметра бочки в чистовых клетях до 1525 мм, а в черновых до 1600 мм и пропорциональном увеличении диаметра шеек поломки были полностью исключены. Следует отметить, что речь о запасе прочности идет без учета остаточных термонапряжений, а они могут серьезно снизить коэффициент запаса. Также отмечены случаи, когда преждевременное разрушение валков происходило вследствие неудачной конструкции перехода от бочки к шейкам, а именно, недостаточного радиуса галтели.
Одна из причин разрушения, связанная с нарушением технологии эксплуатации, - заклинивание полосы в рабочих клетях, при котором возникают большие перегрузки, превышающие номинальные в 3-5 раз. Заклинивание, как правило, происходит за счет неравномерного износа и разогрева валков, а также из-за разрыва полосы. Из всех звеньев технологической цепи наименьшим запасом прочности обладает рабочий валок. Многолетний опыт металлургических предприятий показывает, что при перегрузке наиболее вероятными являются поломки именно рабочих валков [5].
Наиболее частой причиной преждевременного разрушения валков являются недостатки изготовления валков [21]. В первую очередь к ним можно отнести дефекты макроструктуры: зональную и пятнистую ликвацию; внутрикристаллические надрывы; флокены; неметаллические включения; рыхлость; пористость [11]. Отмеченные дефекты возникают в процессе выплавки и разливки стали и могут послужить причиной зарождения и роста трещин. Это особенно актуально при наличии в стали избыточного водорода, что приводит к образованию флокенов - белых по цвету сфероидальных объемов металла, обогащенных протонами водорода [23]. Последующие технологические операции ковки и предварительной термической обработки направлены на устранение указанных дефектов и удаление избыточного водорода из поковок. Однако, как показывают методы неразрушающего контроля (МНК), избавиться от них до конца не удается.
К недостаткам изготовления валков также относятся дефекты микроструктуры: карбидная или ферритная сетка по границам зерен; структурная неоднородность; наличие крупноигольчатого (неотпущенного) мартенсита, наиболее склонного к замедленному разрушению [24]. Перечисленные дефекты являются следствием неправильного выбора или отклонения от технологии режимов ковки и термической обработки.
Основной недостаток изготовления - высокий уровень термонапряжений после проведения окончательной термической обработки. Указанные напряжения возникают вследствие высоких градиентов температур и объемных деформаций, вызванных протеканием структурных превращений.
Практика производства и эксплуатации прокатных валков показывает, что их разрушение до эксплуатации или сразу после завалки в клеть при холодной прокрутке (без нагрузки) происходит с образованием хрупкого излома [5]. Часто в зоне излома наблюдается незаварившаяся при ковке несплошность. Причиной разрушения в этом случае, по-видимому, являются высокие растягивающие остаточные напряжения, повлекшие страгивание трещиноподобного дефекта металлургического характера.
Таким образом, недостатки изготовления в первую очередь влияют на прочность валков как до начала эксплуатации, так и после. Ясно, что конструктивные недоработки и нарушения технологии эксплуатации могут не привести к разрушению валка в случае отсутствия в нем внутренних дефектов недопустимых размеров и высокого уровня остаточных напряжений. Поэтому эти два показателя в основном определяют качество прокатного валка при условии выполнения требований по твердости.
Для своевременного обнаружения недостатков изготовления в технологическом процессе предусмотрены различные виды пооперационного и итогового контроля качества валков. Одним из видов пооперационного контроля является определение твердости после предварительной термической обработки. При этом выборочный контроль производится для отжига или двойной нормализации, а поштучный - для улучшения. После окончательной термообработки осуществляется итоговый контроль с использованием склероскопа Шора [25].
Для выявления поверхностных дефектов окончательно изготовленных валков, таких, как мелкие волосовины ковочного характера; продольные и поперечные трещины, связанные с индукционной закалкой; сетки трещин шлифовочного происхождения, используют токовихревой, магнитопорошковый или капиллярный методы [11].
Токовихревой метод основан на регистрации изменений электромагнитного поля, возникающих вследствие зависимости магнитных свойств стали от ее структурного состава [26]. Метод позволяет выявлять трещины на глубине 0,1.. .0,2 мм величиной 1.. .2 мм. Недостатками метода являются большая масса приборов и длительность исследования (8 ч на валок длиной 1500 и диаметром 300 мм [25]).
Магнитопорошковый метод обладает наивысшей чувствительностью и распознает дефекты, лежащие на глубине 25 мкм размером 2,5 мкм [25]. При наличии дефекта вследствие изменения магнитной проводимости (неметаллические включения) или изменения сопротивления в магнитопроводе (воздушные зазоры при наличии трещины) возникает концентрация магнитных силовых линий [11]. Вокруг дефекта концентрируется взвешенный ферромагнитный порошок окиси железа, который легко обнаружить визуально.
Применение капиллярного метода ограничено и возможно только для хорошо открытых дефектов - трещин [25]. Специальная жидкость при нанесении ее на исследуемую поверхность проникает в трещину и затем вытекает из нее, тем самым указывая расположение дефекта. Для усиления визуального эффекта часто используют проявитель, представляющий собой мелкий порошок, насыпаемый на поверхность [27].
Более опасными, с точки зрения разрушения до начала эксплуатации, являются все же не внешние, а внутренние дефекты. Это объясняется тем, что в поверхностном слое валков после окончательной термической обработки формируются сжимающие остаточные напряжения, а во внутренних областях - опасные растягивающие [28]. Для своевременного выявления внутренних дефектов в прокатных валках широко применяется ультразвуковой контроль (УЗК). В основу метода положено явление акустической эмиссии [27], представляющей собой процесс возникновения в материале акустических волн, излучаемых трещинами. Метод УЗК позволяет выявлять дефекты площадью 6...8 мм2 на глубине 0,5 м и площадью 3...4 мм2 на глубине 0,3 м [29]. На практике нередки случаи образования внутренних дефектов значительных размеров (остатки усадочной рыхлости, расслоения или трещины ковочного происхождения), представляющих опасность разрушения и создающих угрозу обслуживающему персоналу. В связи с этим УЗК применяется в качестве пооперационного контроля, что позволяет обеспечить своевременную отбраковку некачественных заготовок и исключает возможность поставки дефектных валков металлургическим комбинатам.
УЗК, как правило, проводится при горизонтальном положении валка, закрепленного в центрах специальной установки или токарного станка, обеспечивающих его вращение вокруг оси [11]. Поверхность бочки обычно разбивается на участки, соизмеримые с возможностями дефектоскопа. Широко используется дефектоскоп УЗД-7 со щупами поперечных и продольных колебаний. Максимальная глубина, на которую звук проникает в кованые стальные валки при пользовании щупами поперечных колебаний, составляет 1 м, а продольных -2 м. При отсутствии дефектов на рассматриваемом участке валка осцилограмма ультрадефектоскопа начинается и заканчивается пиком, соответствующим входу ультразвука и выходу его в другую среду. Расстояние между этими пиками в определенном масштабе соответствует размерам валка. При наличии дефекта на осцилограмме обнаруживается дополнительный промежуточный пик, месторасположение которого легко определить путем масштабирования [27].
Вопрос о допустимом размере внутреннего трещиноподобного дефекта до конца не изучен и требует подробного рассмотрения в каждом конкретном случае посредством оценки трещиностойкости валка, а именно, возможности разрушения под действием остаточных напряжений при наличии в валке конкретной трещины (размер, месторасположение), выявленной УЗК. Для такого анализа необходимо знать распределение остаточных напряжений по сечению валка.
Экспериментальные методы определения остаточных напряжений делятся на разрушающие (частично или полностью) и не-разрушающие [27]. К полностью разрушающим методам относятся метод Калакуцкого и метод Закса [30], по которым валок вначале разрезается на диски. Затем по методу Калакуцкого производится растачивание вырезанных из диска колец, а по методу Закса - последовательное удаление внешних слоев металла. По изменению размеров судят о величине остаточных напряжений. Следует отметить, что расточка прокатных валков, имеющих после окончательной термообработки большую твердость, представляет значительные трудности. Кроме этого, каждый валок - уникальная дорогостоящая деталь (см. табл. 1.1), и поэтому разрезка его крайне нежелательна и производится только в исключительных случаях.
Наиболее часто для измерения остаточных напряжений в валках используют метод отверстий [27, 31], который считается полуразрушающим, потому что просверленные отверстия глубиной 2...3 мм, равной припуску на механическую обработку, удаляются при окончательном шлифовании. Метод основан на измерении изменения деформаций, вызванного сверлением отверстия в валке. Изменение деформаций можно замерить посредством розетки тензорезистров [27, 31-34], голографической интерферометрии [35], фотоупругости или хрупких покрытий [27]. Зная значения деформаций, произошедших при сверлении отверстий, размеры отверстий и физико-механические характеристики стали, остаточные напряжения можно рассчитать методами теории упругости или по эмпирическим формулам [27].
Главный недостаток рассмотренного метода заключается в том, что определить остаточные напряжения можно только на поверхности валка. К тому же при сверлении отверстий возникают серьезные технические проблемы. Во-первых, должен использоваться инструмент, не создающий дополнительных остаточных напряжений при сверлении. Во-вторых, просверленное отверстие должно быть точно по центру розетки тензодатчиков. Отклонение на 0,025 мм от центра приводит к погрешности, равной 23 % [32].
Из неразрушающих методов контроля остаточных напряжений в прокатных валках используются рентгенографический [36-38], ультразвуковой (акустический) [29] и магнитоупругий [39] методы. Первый метод основан на свойстве кристаллов отражать рентгеновские лучи под определенным углом. В работе [36] значения остаточных напряжений после закалки ТПЧ определены с точностью до 80 МПа. В общем случае погрешность оценки остаточных напряжений при использовании этого метода может достигать 300 % [30]. Кроме того, необходимость специальных мер защиты от облучения, громоздкость аппаратуры и длительность экспозиции (около часа в одной точке) не позволяют широко распространять в производстве данный метод.
Ультразвуковой анализ напряжений основан на зависимости скорости распространения волны от упругих постоянных материала [27]. Согласно этому методу, в валке генерируют волны (продольные или поперечные) и измеряют изменение скорости распространения этих волн в зависимости от уровня напряжений. Указанный метод, так же, как рентгенографический, обладает значительной погрешностью в силу недостаточности данных о взаимосвязи характеристик акустических волн и значений напряжений.
Магнитоупругий метод определения остаточных напряжений [39] заключается в возбуждении в поверхностном ферромагнитном слое валка переменного магнитного потока и измерения изменения магнитной проницаемости стали под нагрузкой. Данный метод, как и первые два, ведет к существенной погрешности [30].
Анализ экспериментальных методов оценки остаточных напряжений показывает, что эти методы чрезвычайно трудоемки и дорогостоящи, обладают значительной погрешностью, а также не позволяют определить временные напряжения, имеющие место непосредственно в процессе термообработки. Следует отметить, что при индукционной закалке ТПЧ эти напряжения могут быть более опасными, чем остаточные [27]. В связи с чем актуальность проблемы определения термических напряжений расчетным способом очевидна.