Пористые сетчатые материалы
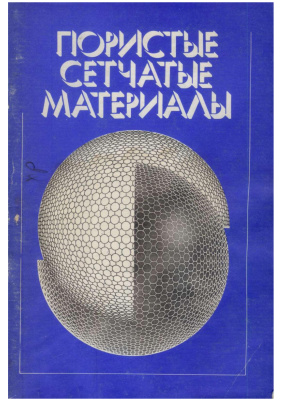
Синельников Ю.И. и др.
Металлургия, 1983 г.
ПРИМЕНЕНИЕ ПОРИСТЫХ СЕТЧАТЫХ МАТЕРИАЛОВ
ПСМ В ФИЛЬТРУЮЩИХ СИСТЕМАХ
Надежная работа гидро- и пневмосистем в конструкциях современного машиностроения во многом определяется чистотой жидкостей и газов, применяемых в качестве рабочего тела.
Среди известных способов очистки жидкостей и газов большое распространение получил механический способ отделения твердых частиц с помощью фильтровальных перегородок.
В настоящее время традиционные фильтроматериалы, такие как ткани, войлок, бумага, керамика, стекло, металлические сетки, заменяют пористыми металлокерамическими материалами. Методами порошковой металлургии получают фильтры различной конфигурации с тонкостью очистки 3; 5; 10; 20; 40; 80; 100 мкм.
Над созданием металлокерамических фильтрующих материалов работает ряд организаций.
В Институте проблем материаловедения АН УССР созданы фильтры из железного порошка АПЖМ, из порошков коррозионностойкой стали типа XI7Н12, хрома, алюминия и других материалов.
Горьковским политехническим институтом им. А.А.Жданова разработана технология изготовления фильтров в виде труб из титанового порошка, а в содружестве с рядом отраслевых институтов и Выксунским металлургическим заводом освоено производство фильтровальных лент из коррозионностойких порошков и титана с тонкостью очистки от 40 до 2—3 мкм [40].
Производство металлокерамических фильтров получило широкое распространение за рубежом. Так, в ГДР изготовляют металлокерамические фильтроэлементы из бронзы и меди в виде втулок, плит, дисков; в Чехословакии, Англии, Японии, Франции, ФРГ — наиболее распространены металлокерамические фильтры из сферических порошков бронзы; в США разработаны фильтрующие элементы десяти классов с тонкостью очистки от 1 до 100 мкм на основе порошков из различных металлов и сплавов [ 39, с. 2—5].
Наряду с металлокерамическими фильтроматериалами получили распространение пористые проницаемые материалы с волокнистой структурой. Основным достоинством пористых металлов на основе волокон является сочетание более высоких по сравнению с порошковыми материалами показателей прочности и проницаемости. Это обстоятельство объясняет тот большой научный и практический интерес, который проявляется к этому классу пористых материалов за рубежом и в нашей стране.
Проводятся работы по изучению свойств и внедрению технологии производства пористых волокнистых материалов из спиральновитой проволоки Куйбышевским авиационным институтом [42]; тонких мерных волокон и трикотажных сеток Институтом проблем материаловедения АН УССР [43, 44]; тканых металлических сеток Московским высшим техническим училищем им. Н.Э.Баумана [9].
Исследования фильтровальных характеристик пористых сетчатых материалов (ПСМ) показали, что для получения фильтроматериалов с высокой производительностью наиболее целесообразно применение тканых сеток с квадратной ячейкой.
Экспериментально установлено [45], что расходные характеристики ПСМ, изготовленных из сеток с квадратной ячейкой № 0040, № 0071 (ТУ 14-4-507—74) со степенями деформации до 30—40 %, не уменьшаются. При эъом номинальная тонкость очистки достигает 10 мкм, а временное сопротивление материала на разрыв 120—130 МПа. Увеличение степени деформации при прокатке ПСМ позволяет резко повысить механическую прочность. Как показано в работе [46], увеличение степени деформации более 50 % приводит к нежелательной разнородности пористой структуры: соотношение максимального к среднему диаметру пор возрастает при существенном снижении проницаемости.
Поэтому оптимальной степенью деформации следует считать значение около 50 %, при этом получается фильтроматериал с отношением максимального диаметра пор к среднему не более 1,05 номинальная тонкость очистки равна 10 мкм. Сочетание удовлетворительной прочности и пластичности позволяет изготавливать из листового ПСМ фильтроэлементы сложной конфигурации (рис. 29, а). На рис. 29, б приведены трубчатые фильтроэлементы, полученные на трубосварочном стане АДС 10-60.
Профилирование пористой ленты в трубную заготовку осуществлялось в валках стана по калибровке, применяемой при получении труб из сплошного материала. Сформованная пористая трубная заготовка поступала в сварочный узел, где осуществлялась сварка кромок.
Далее сваренная трубная заготовка поступала на калибровочный участок стана. После калибровки пористая труба разрезалась отрезным устройством на мерные длины. Полученные трубчатые фильтроэлементы (диаметр цилиндров 12—57 мм, толщина стенки 1,5—3 мм) имели пористость 10—40 %.
ГАЗОЗАЩИТНЫЕ УСТРОЙСТВА
Химическая активность металлов вызывает их взаимодействие с ингредиентами атмосферы и прежде всего с кислородом, азотом и водородом, что в значительной степени ухудшает механические и коррозионные свойства сварных соединений. В связи с этим практический интерес представляет разработка устройств, обеспечивающих при сварке защиту разогретого металла от взаимодействия с атмосферой. Надежность газовой защиты зависит от характера истечения газа из сопла горелки.
Как показано в работе [47], эффективная местная газовая защита обеспечивается лишь потенциальным ядром, так как концентрация газа в нем равна исходной и не содержит примесей воздуха. В значительной степени на величину потенциального ядра влияет конструкция газовых горелок. Наиболее совершенными с точки зрения формирования газовой струи являются газовые горелки, геометрия сопла которых выполнена по кривой Витошинского с небольшой цилиндрической частью на выходе [47].
Однако применение сопел даже с улучшенной геометрией канала не дает возможности существенно увеличить площадь защиты зоны дуговой сварки, потому что при большом расходе газа резко возрастает степень турбулизации струи и уменьшается ее начальный участок.
Использование проницаемых сетчатых вкладышей (газовых линз) позволило погасить общую турбулентность струи путем перевода крупномасштабной турбулентности в потоке до газовой линзы в мелкомасштабную, пропорциональную величине ячейки сетчатых вкладышей. В качестве газовых линз были взяты проницаемые перегородки в виде одного слоя сеток М» 32, 60, 90, 100 (ГОСТ 3187-65). 450 (ТУМУ МОС 7197-63) и пористого сетчатого материала 12Х18Н10Т — ПСМ (ТУ-14-1 -2550-78), изготавливаемого Выксунским металлургическим заводом [9].
Анализ расходных характеристик и фотографий структуры вытекающего из сопла потока показал, что сетки с меньшим размером пор обладают большим аэродинамическим сопротивлением и способствуют сохранению потенциального ядра газа на большем расстоянии от кромки сопла. Так, использование в качестве пористого вкладыша одного слоя сетки № 450 или материала 12Х18Н10Т - ПСМ позволяет увеличить длину потенциального ядра в 5—8 раз по сравнению с соплом без вкладышей при тех же расходах газа.
Из опыта эксплуатации газовых горелок следует, что применение одного слоя сетки или набора из них в качестве газовых линз малоэффективно, так как в процессе сварки брызги расплавленного металла, попадая на поверхность сеток, прожигают их, что нарушает оптимальный режим истечения газа из сопла и ухудшает защиту зон сварки.
Эффективность работы горелок с газовыми линзами из материала 12Х18Н10Т—ПСМ исследовалась при наплавке валика на титановую пластину. За количественный показатель эффективности защиты принимали размер неокисленной зоны в направлении оси шва. Испытания проводили при автоматической аргонно-дуговой сварке с использованием стандартных горелок Град 400 с соплами диаметром 14 мм; скорость сварки составляла 5,5-10—3 м/с.
Экспериментальные данные, приведенные ниже, показывают, что эффективная защита сварного соединения при использовании вкладышей из ПСМ может быть обеспечена при вылете электрода до 20 мм, в то время как стандартное сопло не позволяет увеличить вылет электрода более 7 мм при диаметре зоны защиты 10 мм. Возможность получения эффективной защиты при значительных вылетах электрода особенно важна при сварке в трудно доступных местах и т.д.:
Вылет электрода, мм . . . | 4 | 6 | 8 | 10 | 12 | 14 | 16 |
Вкладыш из ПСМ1 . . . . | 19,5 | 17,0 | 15,0 | 13,0 | 12,0 | 11,0 | 10,0 |
Стандартные горелки1 . . | 16,0 | 13,0 | 8.5 | 5.5 | 2.0 | 0,5 | 0 |
1 Величина зоны-защиты, мм.
Применение устройств с изогнутой поверхностью истечения газа позволяет получать зону защиты во много раз больше, чем с плоской поверхностью истечения. На рис. 30 приведено устройство, где при площади цилиндрической поверхности истечения 19 см2 и удалении устройства от поверхности на 10 мм зона защиты составляет 224 см2.
АГРЕГАТЫ СИСТЕМ ТЕРМОРЕГУЛИРОВАНИЯ
Системы терморегулирования аппаратуры должны работать в условиях различной гравитации и давления, иметь небольшую массу и быть высокоэффективными, что достигается благодаря интенсификации процессов теплообмена. Поэтому особое внимание заслуживает применение агрегатов, в которых теплообмен осуществляется благодаря изменению агрегатного состояния хладоагента [48]. В системах терморегулирования могут быть успешно применены тепловые трубы и теплообменники-испарители.
Тепловые трубы не требуют дополнительной энергии на передачу теплоносителя, не имеют движущихся частей, поэтому они являются наиболее надежными устройствами. Кроме того, они имеют высокую эффективную теплопроводность, передают большое количество тепла на значительное расстояние при небольших градиентах температуры вдоль трубы.
Основой успешной работы и высокой эффективности тепловой трубы является совершенство ее капиллярной структуры, которое определяется высокой теплопроводностью в зонах подвода и отвода тепла и небольшим гидравлическим сопротивлением в зоне транспортировки жидкости. Для выполнения этих условий требуется пористый материал, обладающий высокой технологичностью, прочностью, стабильностью гидравлических и теплофизических характеристик.
Значительный интерес для изготовления тепловых труб заслуживает применение комбинированного пористого сетчатого материала, получаемого в процессе сварки прокаткой брикета сеток с листовым компактным материалом. Этот материал обладает высокой технологичностью, что позволяет изготавливать из него последующей формовкой и сваркой тепловые трубы требуемой конфигурации.