Многокомпонентные вакуумные покрытия
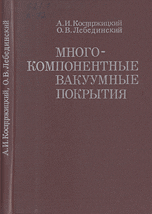
Костржицкий А.И., Лебединский О.В.
Машиностроение, 1987 г.
МЕДНЫЕ И МЕДНО-ЦИНКОВЫЕ ВАКУУМНЫЕ ПОКРЫТИЯ НА СТАЛИ
Покрытия данного типа, полученные в основном методом электроосаждения, широко применяют в различных отраслях народного хозяйства. Принципиально возможно получение покрытий с любым содержанием цинка в сплаве. Основные области применения— декоративная отделка, защита стали от коррозии, использование в виде подслоя под другие покрытия (Ni, Сr и др.), для увеличения адгезии резины к стали, в качестве барьерных слоев в узлах трения (подшипники) и т. п. В гальванотехнике для нанесения медных и медно-цинковых покрытий чаще всего используют цианистые электролиты. Однако в последнее время ведутся интенсивные работы по изысканию возможности применения нетоксичных электролитов. Известен опыт использования тиосульфатных, роданистых, глицератных, триэтаноламиновых, пирофосфатных и других электролитов, широкому промышленному внедрению которых препятствуют высокая стоимость и дефицитность применяемых компонентов, низкая производительность процесса, отсутствие данных производственной проверки.
Сведений о промышленном применении вакуумных покрытий из меди и медно-цинковых сплавов в литературе нет. Вместе с тем основные преимущества метода испарения и конденсации в вакууме, детально рассмотренные в работах [20, 22]» позволяют утверждать, что вакуумные покрытия данного типа применимы во всех случаях, где используют гальванические покрытия и биметаллические материалы с тонким слоем латуни. Успешному внедрению в народное хозяйство медно-цииковых вакуумных покрытий предшествует детальное изучение технологии нанесения покрытия, их физико-химических, механических, защитных и некоторых других свойств. Основные результаты исследований, выполненных в лаборатории ОТИПП в этом направлении, изложены в настоящей главе.
Влияние условии осаждения на структуру и фазовый состав покрытии
Скорость испарения цинка при любых реально возможных температурах на несколько порядков выше скорости испарения меди. Это создает дополнительные трудности при разработке режимов получения покрытий заданного состава. В принципе, для получения покрытий из медно-цинковых сплавов можно использовать все методы, рассмотренные в гл. 1 и 2. Однако обзор научно-технической и патентной литературы, показал, что в настоящее время отсутствуют какие-либо практические рекомендации по нанесению медно-цинковых покрытий в вакууме.
Из всего многообразия параметров вакуумной металлизации, влияющих на характер формирования покрытий [20, 22]. можно выделить три основных: температуру конденсации fK, скорость конденсации υκ и толщину покрытий h. Изменение νκ и hв широком диапазоне их значений не изменяет существенно структуру конденсатов. Определяющее влияние оказывает температура конденсации, а для многокомпонентных систем — и состав покрытий.
При получении медно-цинковых покрытий методом насыщения в парах (см, гл. 2) качество покрытия определяется адгезией и структурой медного слоя. При изучении этих параметров применена методика, суть которой — нанесение покрытий на стальной образец переменного сечения, нагреваемый электрическим током. Это позволяет за один цикл напыления получать набор покрытий при различных температурах, т. е. исключить влияние других факторов на характер формирования структуры. Исследования выполнены в интервале температур 350—900°С. Установлено, что при средней скорости конденсации покрытий на холодную подложку ук=4 мкм/мин критическая температура срыва конденсаций 855 °С. Надежное сцепление покрытия со сталью фиксируется при температуре выше 400 X (см, п. 2).
Исследования продольной структуры медно-цинковых покрытий в интервале температур конденсации 80—120 °С показали, что размер зерен составляет 0,3—1,0 мкм. Структура поперечных шлифов также отличается мелкокристалличностью и однородностью. В диапазоне i«= 150,..330°С покрытия с содержанием цинка до
40% представляют собой обычную латунь (α-фаза); размер зерна увеличивается по мере роста tK(табл. 6). Изменение фазового состава покрытии с изменением /к, в свою очередь, связано с составом конденсата. Для покрытий, осажденных при температуре до 240 °С, характерно образование только α-фазы на основе меди. При более высоких температурах начинают появляться соединения, характерные для β-фазы (CusZrigи др.). При этом с ростом содержания цинка в покрытии фазовые превращения происходят при более низких температурах. Характерно, что размеры зерен интерметаллических соединений CuZnи Cu5Zn8 существенно отличаются от размеров зерен α-фазы и значительно меньше изменяются, чем размеры зерен α-фазы. При температуре 240 °С размер зерна соединений составляет 0,1—0,5 мкм, а при 330 °С возрастает до I мкм.
Покрытия, содержащие более 45 % Zn, состоят в основном из β-фазы (соединения CuZnи Cu5Zn8). Эти соединения характеризуются повышенной хрупкостью, склонны к растрескиванию и промышленного интереса не представляют.