Методы испытаний электролитических покрытий
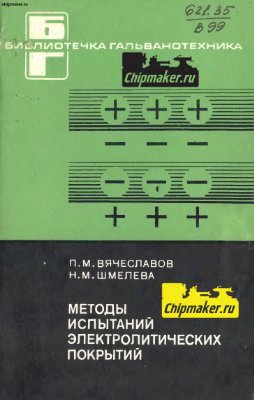
Вячеславов П.М., Шмелева Н.М.
Машиностроение, 1977 г.
КАЧЕСТВЕННЫЕ МЕТОДЫ ОПРЕДЕЛЕНИЯ ПРОЧНОСТИ СЦЕПЛЕНИЯ
Методы основаны на различии физико-механических свойств металлов покрытий и основного металла детали. Большинство качественных методов основано на сильной деформации образца, при которой происходит разрушение покрытия или основного металла. Метод контроля выбирают в зависимости от металла покрытия, вида и назначения детали. Для контроля допускается применять оборудование и приспособления различных типов (полировальные и крацевальные станки, муфельные печи, тиски и т. п.).
Метод полирования.
Поверхность покрытия полируют не менее 15 с. Для полирования применяют круги из бязи, фетра и других материалов, пасты — крокусную, хромовую и др. Скорость полирования — 20—30 м/с. После полирования на контролируемой поверхности не должно наблюдаться вздутия или отслаивания покрытия.
Метод крацевания.
Поверхность покрытия крацуют не менее 15 с. Для крацевания применяют стальные и латунные щетки (для мягких покрытий) с диаметром проволоки 0,1—0,3 мм; частота вращения 1500—2800 об/мин. После крацевания на контролируемой поверхности не должно наблюдаться вздутия и отслаивания покрытия.
Метод навивки.
Метод применим для определения прочности сцепления покрытий на проволоке. Проволоку диаметром до 1 мм навивают на стержень утроенного диаметра; диаметром более 1 мм — на проволоку того же диаметра таким образом, чтобы образовалось 10—15 плотно прилегающих друг к другу витков. Пружины диаметром проволоки до 1 мм контролируют выпрямлением; диаметром более 1 мм — растягиванием пружины на двойную их длину. После контроля на поверхности покрытий не должно наблюдаться отслаивания покрытия.
Метод нанесения сетки царапин.
На поверхность контролируемого покрытия стальным острием наносят 4—6 параллельных линий, глубиной до основного металла, на расстоянии 2,0—3,0 мм друг от друга и 4—6 параллельных линий, перпендикулярных к ним. Линии следует проводить в одном направлении. На контролируемой поверхности покрытия не должно наблюдаться отслаивания.
Метод изгиба.
Детали с покрытием подвергают изгибу под углом 90° в обе стороны до излома. В месте излома покрытие не должно отслаиваться.
Метод вдавливания.
При проверке пригодности листового материала к глубокой деформации (штамповка) применяют пресс Эриксена. Результаты испытаний считают хорошими, если трещины появляются при одинаковой глубине вдавливания на покрытом и непокрытом образцах, причем при образовании трещин на покрытом образце не обнаруживается отслаивания покрытия от основы.
Метод распиловки.
При распиловке образца не должно наблюдаться отслаивания покрытия в месте распиловки. Целесообразно спиливание кромки вести таким образом, чтобы направление штрихов напильника содействовало отрыву покрытия от основного металла.
Метод удара.
Для оценки сцепления используют боек, падающий с определенной высоты. Прочность сцепления тем выше, чем больше ударов бойка выдерживает испытуемый участок поверхности до отслаивания.
Метод трения.
В пробах, подвергнутых высоким нагрузкам, от трения в процессе испытания образуется значительное количество теплоты. Эта теплота вызывает расширение как основного материала, так и его покрытия. Если коэффициенты линейного расширения обоих металлов в значительной степени отличаются друг от друга, в местах с плохим сцеплением может произойти вспучивание покрытия, образование пузырей, и покрытие может отслоиться.
Этот метод испытания не зависит от геометрической формы образца, однако он подвержен влиянию скорости трения и влиянию давления, в результате которых создается нагрузка трения.
Метод нагрева.
Этот метод основан на тех же физических основах, что и предыдущий. Детали с покрытием нагревают в течение 0,5—1,0 ч и охлаждают на воздухе. Температура нагрева (° С) деталей со всеми видами покрытий, за исключением цинковых, кадмиевых, оловянных, свинцовых, сплавом олово—свинец, следующая:
Алюминий и его сплавы 190±5
Магний и его сплавы 125±5
Медь и ее сплавы 250±5
Сталь и чугун 350±5
Титан и его сплавы 210±5
Цинк и его сплавы 140±5
Допускается понижение температуры нагрева для деталей, имеющих швы, паяные припоями с температурой плавления ниже температуры нагрева, указанной выше. Для цинковых и кадмиевых покрытий температура нагрева должна быть 180—200° С; для оловянных, свинцовых и покрытий сплавом олово—свинец— 140—160° С. После нагрева на контролируемой детали не должно быть вздутия или отслаивания покрытия.
Электрохимические методы.
Для изучения прочности сцепления плотных покрытий в том случае, когда ток в начале электролиза не расходуется на побочные реакции и целиком идет на восстановление ионов металла, может быть использован электрохимический метод. Сущность метода заключается в том, что на основании значения поляризации в момент включения тока определяется активная часть поверхности катода, на которой происходит осаждение металла, что и характеризует степень сцепления электролитического покрытия. Пробу в качестве катода помещают в электролит, из которого происходит осаждение металла покрытия без побочных реакций (выход металла по току 100%) необычными способами измеряют поляризацию электрода.
В тех случаях, когда в момент включения тока поляризация имеет повышенное значение, уменьшающееся со временем электролиза электрохимический метод однозначно указывает на плохую сцепляемость. В случае же отсутствия повышенного значения поляризации в момент включения тока имеет место хорошее сцепление покрытия с основой при условии, что весь ток расходуется на осаждение металла.
Другой электрохимический метод заключается в следующем: пробу в качестве катода помещают в электролит, состоящий из 5%-ного раствора едкого натра или едкого кали при относительно высоком напряжении на ванне (около 10 В). Выделенный на катоде атомарный водород диффундирует сквозь покрытие, скапливается в местах дефектов на пограничной поверхности, при продолжительном насыщении образует пузыри. Если покрытия выдерживают продолжительность насыщения водородом более 15 мин без образования пузырей, можно считать, что они имеют хорошее сцепление с основой.
КОЛИЧЕСТВЕННЫЕ МЕТОДЫ ОПРЕДЕЛЕНИЯ ПРОЧНОСТИ СЦЕПЛЕНИЯ
Все количественные методы испытания основываются в большей или меньшей степени на определении силы, необходимой для отрыва покрытия от его основания или для его срезывания. Прочность сцепления выражается частным от деления отрывающей или срезывающей силы на площадь сцепления. Количественные методы измерения по сравнению с качественными имеют преимущества, так как измеряют абсолютные величины, хотя применение их в производственных условиях и сдерживается трудностью изготовления специальных образцов и дороговизной испытательных станков.
Методы отрыва.
Один из них — метод Е. Олларда — заключается в осаждении металла на торцевую часть цилиндрического образца 3 и последующем отделении покрытия на разрывной машине. Путем деления силы, необходимой для отрыва, на площадь можно определить силу сцепления покрытия с основным металлом. Недостатки такого способа заключаются в необходимости осаждения толстых покрытий, пригодных для испытания, и сложности подготовки катода после электролиза к испытанию, так как катод обрабатывается на станке для получения выступающих краев покрытия, за которые он удерживается при испытании на разрыв.
Метод Жаке схож с описанным выше методом Олларда. Разработан он для никелевых покрытий по стали. Плоский никелированный образец определенных размеров частично погружают в специальный раствор, который при последующем омеднении понижает сцепление электролитического слоя меди в смоченных этим раствором местах (применяется раствор протеина). Толщина медного слоя должна быть не ниже 300 мкм.
По этому методу участок медного покрытия с ослабленным сцеплением отгибают под прямым углом и определяют перпендикулярно к поверхности образца силу, необходимую для отрыва никелевого покрытия от основного металла. Метод основан на том, что сцепление между электролитическим слоем меди и никелевым слоем значительно больше, чем между никелевым слоем и сталью. По этому методу испытывают медные слои печатных плат, нанесенные на синтетические материалы. В практике метод применяют и для других металлических покрытий.