Магниево-литиевые сплавы
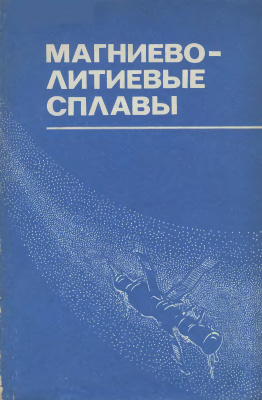
Дриц М.Е. (ред.)
Металлургия, 1980 г.
Первые исследования магниево-литиевых сплавов (25, 26] показали, что для стабильного обеспечения высоких прочностных и пластических свойств, а также технологичности в сочетании с пониженной плотностью желательно, чтобы эти сплавы имели двухфазную структуру, легированную дополнительно алюминием, цинком, серебром и кадмием. Наибольшее влияние на стабильность свойств этих сплавов оказывают добавки серебра. В этой же работе указывалось на заметную чувствительность предела текучести сплавов (а + β) и скорости нагружения и незначительное упрочнение их при холодной деформации. Так , предел текучести сплава Mg — 9% Li — 4% Zn (145 МПа) можно было повысить только до 155 МПа путем обжатия на 75% при холодной прокатке.
Фрост с сотрудниками [54] исследовали старение сплавов системы Mg—Li—AI, содержащих от 7,7 до 10% Li и легированных порознь марганцем, цинком или оловом. Полученные данные показали, что стабильность свойств повышалась с увеличением количества a-фазы; добавки олова оказывали благоприятное влияние на стабильность свойств сплава, прочность и на стойкость к коррозии под напряжением. Рекомендованы две системы на основе (а + β) -фаз высокопрочных сплавов: Mg—Li—Al—Sn и Mg—Li—Al—Zn.
M.E. Дриц, З.А. Свидерская и В.Ф. Трохова подробно исследовали влияние различных легирующих добавок на структуру и свойства сплавов Nfe — (7—10%) Li [49]. На рис. 15 приведены графики, характеризующие влияние некоторых элементов на механические свойства сплава Mg— 8% Li — 5% AI в горячепрессованном и стабилизированном (100°С, 100 ч) состояниях. В результате проведенных исследований лучшее сочетание прочностных свойств и пластичности было достигнуто для двух композиций сплавов [5—57]: 1) Mg — (7-10) % Li—(4-6)% Аl— (3-6)% Cd- (0,8-2,0)% Zn - (0,15-0,5)% Mi (сплав ИМВ2); 2) Mg- (7-9)% Li - (4-6)% Al - (2-4)% Sn - (0,8-2,0)% Zn - (0,15-0,5)% Mn (сплав ИМВ2-1). Температуры начала и конца рекристаллизации обработки сплавов ИМВ2 и ИМВ2-1 соответственно 245—360 и 270—380°С.
Приведенные данные показывают, что для всех исследованных сплавов наиболее нестабильны значения предела текучести, который уменьшается на 10—25 МПа. Свойства сплава ИМВ2 были наиболее стабильны по сравнению со сплавами ИМВ2-1 и Mg — 8% Li — 5% А1.
Исследование микроструктуры сплавов ИМВ2 и ИМВ2-1 и влияния отдельных легирующих добавок [49J на их свойства показало, что основным фактором, обеспечивающим достаточно высокий уровень прочностных свойств этих многокомпонентных сплавов, является наличие а- и /3-фаз сложного состава. Такие элементы, как алюминий, цинк, олово и марганец, помимо усложнения а- твердых растворов, образовывали самостоятельные фазы (Al, Zn)Li, Mn—А1—Fe, Sn -Mg, причем структура сплава ИМВ2-1 была более гетерогенной, чем сплава ИМВ2 (рис. 16).
В работах [58—60] было показано, что сплавы ИМВ2 и ИМВ2-1 могут быть существенно упрочнены в результате холодной деформации, полной термической обработки и особенно НТМО. Выполненная в лабораторных условиях НТМО прессованных прутков из сплава ИМВ2 по режиму: закалка (380°С, 1 ч, холодная вода) + холодная деформация растяжением на 2,5%+естественное старение повышает прочность на 100—150 МПа, причем по данным работы [60] это упрочнение достаточно стабильно как при длительной (6 мес.) выдержке при комнатной температуре, так и после нагревов при 60 и 100°С до 200 ч (рис. 17). Следует отметить, что прочностные свойства, эффект упрочнения и его стабильность у сплава ИМВ2 были выше, чем у сплава ИМВ2-1.
В лабораторных условиях [61] исследовано влияние высокотемпературной термомеханической обработки (ВТМО) на механические свойства и структуру сплава ИМВ2. Обработка заключалась в нагреве слитков до 325—400°С в течение 1 ч, подстуживании на воздухе до 100, 125, 150, 175, 200, 225, 250°С и прессовании в прутки диаметром 10 мм со степенью деформации 87%. Анализ полученных результатов позволил выбрать оптимальный режим ВТМО: нагрев до 350—375°С, подстуживание до 150°С и деформация при этой температуре. Изготовление прутков по указанному режиму позволило повысить их прочностные свойства на 30—50 МПа как в горячепрессованном, так и в стабилизированном (175°С, 6 ч) состояниях по сравнению со свойствами прутков, полученных прессованием по принятой технологии при 250—300°С.
Добавка в магниевые сплавы более 10,4% Li весьма перспективна, так как дает возможность получить самый легкий металлический конструкционный материал (плотность 1300— 1500 кг/м3) на 20—30% легче стандартных магниевых и в 2 раза легче алюминиевых сплавов. М.Е. Дрицем, З.А. Свидерской, Ф.М. Елкиным были выполнены обширные исследования по установлению связи между составом, структурой и свойствами магниево-литиевых сплавов на основе 0-фазы [49]. Результаты этих исследований по легированию сплава Mg —14% Li представлены на рис. 19.
Наиболее интенсивно (в 2—3 раза) увеличивалась прочность и понижалась пластичность при вводе 1,5—2,5% А1 и до 10% Zn. Добавки Cd, Ag, Si, Nd, Sn, Cu, La, Ce, Y в количестве 2—10% увеличивали прочность на 15—25%, легированные сверхлегкие богатые литием сплавы на основе систем: Mg—Li—Zn—Al—Mn—Се — сплав ВМД5, Mg—Li— Zn—Sn — сплав ИМВЗ и Mg—Li—Zn—Al—Sn — сплав ИМВ4 [67, 68). Состав и некоторые физико-механические и технологические свойства указанных выше сплавов в сравнении с аналогичным американским сплавом LA141A, полученных в одинаковых условиях, приведены в табл. 6.
Сравнительное опробование сплавов ВМД5, ИМВЗ, ИМВ4, а также сплава LA141A показало, что оптимальным сочетанием физико-механических, технологических и коррозионных свойств обладает сплав ВМД5, который в настоящее время и получил промышленное использование. Свойства и структура сплава ВМД5 (МА18) подробно изложены в разделах 5,7, 8, 9.
Ниже по данным зарубежных источников [62—64] достаточно подробно освещены свойства единственного стандартного за рубежом магниево-литиевого сплава LA141A (США), а также некоторых других сплавов на основе /3-фазы, опробованных или применяющихся в США.
В результате исследований, проведенных в США и Англии по изучению влияния легирования и термической обработки на свойства магниево-литиевых сплавов, пришли к заключению, что оптимальным сочетанием удельной прочности и жесткости, пластичности и ударной вязкости обладают сплавы, содержащие 13—15% Li и до 10% суммы других легирующих элементов (Al, Zn, Cd, Ag и Si). Низколегированные магниеволитиевые сплавы по сравнению с высокопрочными сплавами, содержащими большое количество упрочняющих добавок, обладали значительно меньшей прочностью в стабильном состоянии (σв = 130^180 МПа; σ0 2 = 10СН-150 МПа). Однако они имели повышенные пластичность и ударную вязкость (S = 1СН- *60%, ан = 15СН-550 кДж/м2), хорошо обрабатывались давлением в холодном и горячем состояниях и хорошо сваривались при комнатной температуре, допустимая степень деформации большинства этих сплавов была не менее 75—80% (25, 56].
Одним из лучших низколегированных сплавов был американский сплав LA142, улучшенная модификация которого — стандартный сплав LA141A — находит наиболее широкое использование в различных областях новой техники в США [62—65]. Первоначально в США был разработан сплав Mg — (13-M5)Li — (5г7)А1 — (0,1-г0,3) Мn, однако он обладал пониженной свариваемостью. Уменьшение содержания алюминия и марганца в сплаве и ограничение количества примесей, в частности натрия, позволили рекомендовать для промышленного производства сплав LA141A. Состав этого сплава, по данным основных организаций, которые выпускают его или применяют, приведен в табл. 7. Внесенные изменения позволили улучшить свариваемость, уменьшить охрупчивание, увеличить сопротивление коррозии и повысить технологическую пластичность сплава.
Полуфабрикаты из сплава LA141A по стандарту LAC07 — 4194А поставляются заказчику после закалки при 288°С (нагрев 1 ч на толщину 25 мм, но не менее 1 ч), охлаждения на воздухе и стабилизирующего старения при 177°С в течение 2—6 ч.
По стандарту АМS 4386 листы и плиты стабилизируются по режиму 166—190°С (177±14°С) 3—6 ч без предварительной закалки и травятся в кислоте (состояние Т7).