Контролёр работ по металлопокрытиям
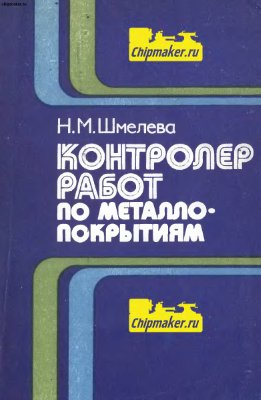
Шмелева Н.М.
Машиностроение, 1980 г.
§ 1. КВАЛИФИКАЦИОННЫЕ ТРЕБОВАНИЯ К КОНТРОЛЕРАМ РАЗЛИЧНЫХ ПРОФЕССИЙ
К контролерам машиностроительных заводов предъявляют определенные квалификационные требования, отнесенные к соответствующему разряду работ и предусмотренные тарифно-квалификационными справочниками.
Общими являются следующие требования, предъявляемые к контролерам всех профессий и разрядов.
Контролер должен знать наименование и номера принимаемы;' изделий; технические условия или технологию контроля на принимаемую продукцию; наименования и номера измерительных инструментов, необходимых для контроля, и правила пользования ими; технологию изготовления контролируемых изделий; основные виды брака, свойственные этим изделиям; правила по технике безопасности при контроле.
Контролер должен уметь различать наружным осмотром внешние дефекты и пороки в изделиях; пользоваться средствами контроля; читать чертежи на принимаемую продукцию; правильно подразделять контролируемые изделия на «годные», «дефектные», «брак»; правильно оформлять документацию на принятые и забракованные изделия.
Конкретные требования к контролерам разных профессий изложены в соответствующих квалификационных характеристиках в зависимости от разряда. Для контролера работ по металлопокрытиям 3-го разряда квалификационная характеристика выглядит следующим образом.
Контролер по металлопокрытиям 3-го разряда должен уметь контролировать и принимать сложные детали и изделия после металлопокрытия с труднодоступными для проверки местами с применением дополнительных катодов, анодов и экрана; определять толщину- слоя металлопокрытия при помощи контрольно-измерительных приборов; проверять контрольные размеры, указанные в чертежах и технологических картах; проверять заданные режимы осаждения металлопокрытия по показаниям контрольно-измерительных приборов; контролировать силу тока, температуру электролитов, качество полирования и глянцевания; проверять правильность установки дополнительных анодов; контролировать правильность монтажа деталей для покрытий; проверять степень шероховатости основного металла; определять пригодность деталей для покрытия; осуществлять внешний осмотр детален и выявление дефектов основного металла, пороков сварки и других дефектов поверхности, которые могут привести к забракованию деталей после покрытия; отбирать пробы материалов для проведения химического анализа, механических и металлографических испытании; различать виды брака контролируемой продукции и вести первичный технический учет дефектов и причин брака; оформлять документы на принятую и забракованную продукцию; правильно организовать и содержать рабочее место, экономно расходовать материалы, инструменты и электроэнергию; применять наиболее целесообразные и производительные способы работы и современные методы организации труда; выполнять правила техники безопасности, электро- и пожарной безопасности, гигиены труда и внутреннего распорядка.
Контролер по металлопокрытиям 3-го разряда должен знать технические условия и ГОСТы на приемку сложных изделий и деталей до и после покрытия; технологический процесс полирования, глянцевания и нанесения металлопокрытии; методы контроля покрытий; устройство, назначение и условия применения контрольно-измерительных инструментов и приборов; классификацию и виды брака при металлопокрытиях; методы профилактики брака; назначение, составы, свойства и правила обращения с реактивами и электролитами, употребляемыми для металлопокрытий; допуски, посадки, классы точности и шероховатости поверхности; методы нанесения всех видов металлопокрытий; требуемую степень шероховатости поверхности и толщину слоя металлопокрытия; первичные документы по учету годной и забракованной продукции; структуру ОТК, взаимоотношения с другими отделами и цехами предприятия; права и обязанности контролера; сведения по механизации и автоматизации производства и контроля; основы экономики труда и производства; правила внутреннего распорядка, техники безопасности, электро- и пожарной безопасности; основы гигиены труда и промышленной санитарии.
§ 2. РАЦИОНАЛЬНЫЕ ПРИЕМЫ В РАБОТЕ КОНТРОЛЕРА
При планировке цехов технологический отдел завода предусматривает удобное движение продукции с одной операции на другую, через промежуточные контрольные пункты к окончательному контролю. Контрольные пункты располагают рядом с обслуживаемым производственным участком по ходу технологического процесса изготовления изделий.
Рабочее место контролера должно быть по возможности ограждено от производственного оборудования и не мешать движению транспорта; иметь правильное и достаточное освещение. Контрольную оснастку следует располагать под рукой, чтобы не было неудобств при работе. Все эти условия необходимо соблюдать как при промежуточном, так и при окончательном контроле изделий.
Совершенно недопустимо захламлять рабочее место контролера, бессистемно располагать контрольно-измерительный инструмент, так как это снижает производительность труда контролера, влечет за собой неправильную оценку качества продукции и является причиной пропуска дефектных деталей.
Контрольно-измерительные инструменты и приборы, которыми пользуются во время работы, следует располагать на рабочем месте контролера в порядке последовательности их применения, на строго определенных местах. В непосредственной близости должны» находиться инструменты и приборы, которыми контролер пользуется чаще всего.
Подлежащие контролю изделия, как правило, устанавливают на столе приемки по несколько штук в удобном для контролера положении. При таком расположении контролируемых изделий и измерительного инструмента контролер может выполнять самые короткие движения и поэтому работать более производительно.
При проектировании рабочих мест контролеров и их оснастки необходимо внимательно изучить условия труда на данном участке, чтобы создать максимальные удобства для контролера, облегчить его труд, устранить причины, вызывающие утомление, и повысить производительность.
Во время работы, особенно при поточной подаче изделий на контрольную точку, контролер затрачивает много мускульной энергии. Чем напряженнее поза контролера во время проведения измерительных операций, тем быстрее он утомляется и, следовательно, становится менее работоспособным и внимательным. В связи с этим на рабочем месте для контролера должно быть обеспечена удобное положение, для чего устанавливают несложные приспособления, которые устраняют напряжения и, следовательно, избавляют контролера от преждевременного утомления.
Летучий или статистический контроль изделий производится на рабочих местах; в этом случае основная работа контролера в течение смены не связана с подачей на контроль продукции. Рабочее место контролера при этом оборудуют всем необходимым для хранения инструмента, приборов, оформления документации.
Рабочее место контролера должно быть достаточно освещено. Требуемая освещенность для контроля металлопокрытий — не менее 300 лк. В настоящее время для промышленного освещения получили распространение люминесцентные лампы. Важность освещения рабочего места контролера наглядно подтверждает следующий пример. На одном машиностроительном заводе в течение нескольких лет применяют комбинированный способ освещения контрольных участков ОТК на приемке луженых металлических деталей. Основные виды брака таких деталей: царапины, наплывы, наличие мест, не покрытых оловом, образование крупинок олова и др. Часто эти дефекты могут быть весьма малы и при недостаточном освещении трудно различимы. Под большим колпаком молочного цвета помещают лампу ртутную газосветную мощностью 500 Вт и лампу накаливания мощностью 150 Вт.
§ 3. МАРКИРОВКА И КЛЕЙМЕНИЕ ПРОДУКЦИИ
Клеймение продукции, входящее в круг обязанностей работников технического контроля, производят при операционной и окончательной приемке деталей, узлов, агрегатов собранных и испытанных машин.
Маркировка предусматривает нанесение на деталь или прикрепленный к ней ярлык условных знаков, обозначающих марку, сорт, технические характеристики и т. д. Маркировка в большинстве случаев является производственной операцией, контролируемой работниками ОТК-
Наличие клейма показывает, что деталь или изделие прошли определенные операции, приняты техническим контролем и годны для дальнейшей обработки, сборки, испытания или выпуска с завода. Клеймение предусматривает персональную ответственность лица, поставившего клеймо за годность продукции.
После определенных операций клеймо наносят в соответствующих местах изделий и агрегатов согласно указаниям, предусмотренным в чертежах или технологических картах. Место, выбранное для клейма, должно обеспечивать отчетливый оттиск, не должно находиться на базовой поверхности, должно сохраняться до окончательной приемки и по возможности оставаться открытым при сборке. Неудачный выбор места для клейма или неправильное пользование клеймом могут быть причиной брака или повреждения изделия.