Кобальт и никель
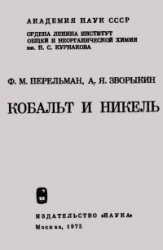
Перельман Ф. М., Зворыкин А. Я.
Наука, 1975 г.
Получение металлического кобальта
Для получения металлического кобальта его окись должна быть восстановлена. Наиболее распространены методы восстановления окиси кобальта углем. Именно этим путем впервые был получен металлический кобальт Тассаэртом еще в конце XVIII в. (см. [1]). Он смешивал окись кобальта с маслом, крахмалом или пшеничной мукой, пересыпая смесь древесным углем и нагревал до темно-красного каления. При этом получалась металлическая губка, легко рассыпавшаяся в порошок и содержавшая небольшое количество углерода (его можно удалить, сплавляя металл с окисью кобальта).
Муассан получал твердый и хрупкий металлический кобальт с 4% углерода восстановлением окиси кобальта винным камнем в графитовом тигле.
Систематические опыты по восстановлению Со304 антрацитом, древесным углем и сажей дали следующие результаты. Восстановление антрацитом малопригодно, так как для полноты реакции требуется вести процесс не менее 1 час при температуре, близкой к 1200° С. С древесным углем и сажей восстановление идет значительно быстрее и при более низких температурах. Так, при избытке угля в 20—30% против теоретического (исходя из уравнения 2Со304 + 4С =6Со + 4СO2 ) полное восстановление окиси наступает после прокаливания в течение 1 час при 900° С и в течение 10 мин при 1000° С. От избыточного угля полученный металл освобождают магнитной сепарацией [287].
Таким образом восстановление окислов кобальта углем протекает в твердом состоянии. Как показали Тамман и Зворыкин [269], начало восстановления СоО находится около 650° С, т. е. не только задолго до температуры плавления, но и до температуры спекания, которая, по данным тех же авторов, равна примерно половине значения температуры от абсолютного нуля до точки плавления. При восстановлении окислов кобальта углем в заводских условиях равновесие не достигается, и реакция идет с выделением окиси углерода.
Металлический кобальт с низким содержанием углерода можно получить, если вести восстановление брикетированной с углем окиси в вольтовой дуге. Тогда электроды-брикеты плавятся, и восстановленный металл стекает в тигель. От окисления его защищают шлаком из окиси кальция и кремнекислоты.
Восстановление окиси кобальта можно вести также водородом. В этом случае процесс протекает ступенчато: сначала образуется низший окисел при характерной минимальной температуре, а затем с повышением температуры — он восстанавливается до металла.
Муассан (см. [1]) полагал, что температура начальной реакции не превышает 190—200° С и что при 250° С образуется пирофорный кобальт. Процесс восстановления идет быстрее по мере повышения температуры реакции, как видно из табл. 17.
Охлаждение металла необходимо вести в атмосфере водорода, иначе он вновь окислится. Металл, полученный восстановлением окислов кобальта водородом, часто обладает высокой каталитической активностью в некоторых реакциях, особенно если восстановление гало при повышенном давлении, 20—40 атм (в этом случае процесс идет уже при 100° С).
Окислы кобальта можно восстановить до металла также с помощью окиси углерода: между Со3O4 и СО реакция начинается уже при 300° С, а при 500—750° С протекает интенсивно и за несколько минут восстанавливается до 90% исходной окиси. Однако остальные 10% реагируют очень медленно даже при 900° С.
Для получения металлического кобальта из его окислов можно применить алюмотермию. Реакция сильно экзотермична и протекает по уравнению
3Co3O4+8А1=4А12O3 + 9Со.
При этом температура повышается до 2100° С.
Кроме того, металлический кобальт может быть получен цементацией из растворов его солей. Давно известно, что кобальт вытесняется цинком и кадмием. Но для полноты реакции и во избежание выделения гидрата окиси кобальта необходимо соблюдать ряд условий. Так, найдено, что выделение кобальта облегчается в присутствии солей меди и отчасти свинца. Для образования плотного слоя металлического кобальта необходимо вести процесс при низкой температуре и в слабокислой среде. Из аммиачного раствора кобальт может быть вытеснен цинком при температуре кипения [2871]
Водород также может вытеснить металлический кобальт из растворов его солей, но лишь при повышенных давлениях: при 100 атм из водных растворов CoSO4 выделяется металлический кобальт (наряду с моногидратом) уже при 140—150° С. Так как температура и давление тем ниже, чем благороднее вытесняемый металл, то этим путем можно отделить кобальт от некоторых его спутников. Имеются данные о том, что вытеснение металлов в этом случае происходит последовательно в ряду Сu—Ag—Ni— Со—Zn[288]. Полученный этим путем кобальт также обладает высокой каталитической активностью.
Наконец, металлический кобальт получают электролизом из аммиачных или азотнокислых растворов [289], а также из нейтрального раствора кобальтовой соли с добавлением сахара или глицерина [290ПСостав ванны оказывает большое влияние на характер и качество кобальтовых осадков [291]. Наилучшие результаты получены при электролизе растворов хлористого кобальта в присутствии фосфорной кислоты и монофосфата натрия [292]. Описан процесс рафинирования рондельного кобальта, содержащего 98,4—98,7% Со, 0,18% Ni, 0,19% Fe, 0,22% CaO, 0,02% Сu, 0,06% Mn, 0,08% С и 0,08% Si. В ходе процесса кобальтовые рондели являлись анодами, а чистый кобальт отлагался на вращающемся катоде из нержавеющей стали. Вращающийся катод обеспечивает равномерное перемешивание электролита и поверхности электрода. Температура электролита 55° С/ скорость вращения катода 60—100 об/мин, рН 4,5—5,0, плотность тока на катоде 4,5 а/дм2.
Расстояние между анодом и катодом равно 38 мм. В более кислых ваннах становится более значительным выделение водорода, а выход кобальта по току понижается, причем металл получается непрочным (отслаивается) и образуется значительное количество гидроокиси кобальта как на катоде, так и на аноде. Повышение температуры допускает большую скорость осаждения, но при этом сильно увеличивается испарение. В изложенных условиях получают слой кобальта толщиной до 3,2 ммпри сравнительно небольшом образовании дендритов. Слой в 0,8 ммполучается ровный, плотный, хорошо пристающий. Такие слои легко снимаются большими пластами.
Электролитически очищенный металл содержит 99,76% Со, 0,005% М и 0,10%) Fe. Электролитический кобальт имеет на поверхности — 0,28% окислов, которые удаляют нагреванием до температуры красного каления в токе водорода. Полагают, что этот метод пригоден для получения чистого кобальта в больших количествах.
В последние годы технология производства кобальта как у нас в стране, так и за рубежом значительно изменилась. Прежде всего, для отделения кобальта взамен гипохлорита натрия стал применяться непосредственно хлор. Кроме того, для растворения кобальтового концентрата взамен серной кислоты используется сернистый газ. В результате изменения технологии и совершенствования аппаратуры достигнут систематический рост выпуска кобальта в результате повышения его извлечения из природного сырья, при непрерывном снижении производственных затрат и повышении производительности труда._
На некоторых производствах сырьем для кобальтового производства служит концентрат электролизного цеха с содержанием 15—16% Со и от 1,3 до 1,6% Ni, а также 2,5—3% Fe. Кроме того, концентрат содержит небольшие количества меди, марганца и других примесей. Этот концентрат подвергают репульпации и затем обрабатывают серной кислотой (25 г/л).
После полного растворения закисное железо окисляется воздухом, а раствор нейтрализуется измельченным известняком до рН 3,5—4,5. При этом окись железа дает легко фильтрующийся крупнозернистый осадок. Дальнейше повышениее рH до 6,0—6,7 ведут содовым раствором, что приводит к выделению в осадок также окиси меди. В результате в растворе остается железа и меди не свыше 0,01 г/л. В то же время в отвальных кеках отношение кобальта к железу не превышает 1 : 50.
После очистки от железа и меди фильтрат направляют на очистку от марганца. Содержание марганца здесь невелико (в 500 раз ниже содержания кобальта). В процессе очистки на 1 кгмарганца расходуется 4 кгхлора; при этом в осадок выделяется также некоторое количество кобальта, так что в первичном марганцевом кеке отношение Со : Мn нередко достигает 10 : 1. Поэтому он подвергается повторной обработке: растворяется в растворе серной кислоты и сернистого газа и из полученного раствора марганец осаждается вторично.
Во вторичном марганцевом кеке отношение Со : Мn составляет от 3 :1 до 1 : 1. Этот вторичный марганцевый кек вновь растворяют серной кислотой и сернистым газом, а в раствор, содержащий 10—20 г/л кобальта и 7— 10 г/л марганца, добавляют раствор каустической соды, что приводит к выделению 90 — 95% первоначального количества кобальта в виде гидрата закиси, в то время как марганец в основном остается в растворе. Этот кобальтовый осадок направляется в голову процесса.
Очищенный от железа, меди и марганца раствор поступает на осаждение гидроокиси кобальта газообразным хлором и смесью кальцинированной и каустической соды (Na2C03 110—120 г/л, NaOH80—90 г/л). Совершенствование методов использования хлора позволили значительно сократить его расходы. Заданное соотношение реагентов поддерживается автоматически. Гидроокись кобальта осаждают при температуре —- 70° С на 90—92% (в зависимости от содержания в растворе никеля), отфильтровывают и направляют на прокаливание. Из фильтрата оставшийся в нем кобальт осаждают кальцинированной содой, и в полученном осадке Со : Ni=10 : 1; оставшийся в фильтрате никель (1,5— 2 г/л) осаждают содовым раствором. Гидроокись кобальта прокаливают при 900° С; температуру регулируют автоматически. В печах имеется система пылеулавливания, поэтому потери кобальта невелики.
Большое количество кобальта извлекается при переработке медно-никелевых и никелевых руд попутно с извлечением никеля; при этом содержание кобальта в исходном сырье составляет 3— 10% от содержания никеля. Было установлено, что при плавке сульфидных медно-никелевых руд до 95% кобальта переходит в медно-никелевый штейн. При его конвертировании 60 — 70% кобальта переходит в конверторные шлаки, главным образом в шлаки последних сливов, которые и служат сырьем для его извлечения. Найдено, что при разделительной плавке файнштейна — 70% кобальта переходит в никелевый полупродукт (боттом) и —30% — в медный полупродукт (топ).
Таким образом, в процессе переработки сульфидных медно-никелевых руд получаются три полупродукта, которые могут служить сырьем для производства кобальта: конверторные шлаки, шлаки от продувки топа и кеки от очистки боттома, причем в конверторных шлаках содержится — 50% от всего количества кобальта при его концентрации 0,4%. Для его извлечения предложен метод, сущность которого состоит в обработке расплавленных конверторных шлаков твердым восстановителем (коксом или антрацитом) над слоем штейна. Заливаемый в электропечь штейн
Служит растворителем образующегося на контакте кокс — шлак металлического сплава. Отвальный шлак, выдаваемый из печи, содержит 0,04—0,06% кобальта и около 50% железа.