Химико-термическая обработка металлов с применением нагрева токами высокой частоты
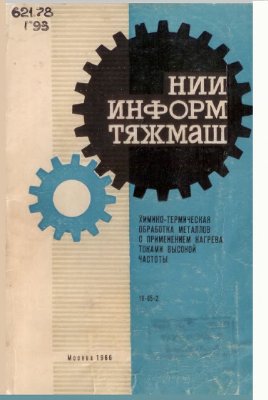
Гугель С.М.
НИИИНФОРМТЯЖМАШ, 1966 г.
ХИМИКО-ТЕРМИЧЕСКАЯ ОБРАБОТКА В ЖИДКИХ СРЕДАХ
Сущность химико-термической обработки в жидких средах заключается в том, что деталь, нагретую ТВЧ, а иногда и индуктор помещают в холодную жидкую среду. В зависимости от химического состава среды происходит тот или иной вид химико-термической обработки.
В 1939 г. М. Г. Лозинский доказал возможность цементации стали, нагреваемой ТВЧ при погружении ее в керосин [27]. Способ зональной цементации в керосине при нагреве ТВЧ был предложен в 1954 г. С. Д. Богословским.
Позднее в Польше был запатентован способ диффузионного насыщения металлов различными элементами, при котором изделие вместе с индуктором помещается в жидкую среду, содержащую-насыщающий элемент.
ЦЕМЕНТАЦИЯ
Эксперименты по цементации в жидких средах проведены на образцах из стали 10 диаметром 7 и длиной 40 мм. Образцы устанавливались в высокочастотном одновитковом индукторе диаметром 9 и шириной 10 мм. Нагрев осуществлялся от генератора ГВ-21 .мощностью 20 кет и частотой 450 кгц. В качестве насыщающей среды использовалась нефть и керосин. Однако вследствие значительного содержания непредельных углеводородов, при нагреве на поверхности образцов выделялся толстый слой кокса, препятствующий проникновению углерода к поверхности металла. Использование метилового спирта показало положительные результаты. При выдержке в течение 10 мин и температуре 800, 900, 1100 и 1200° получена глубина диффузионного слоя, соответственно, 0,15; 0,43; 0,60; 0,70 и 0,78 мм.
Оптимальной считается температура 800—1000°С, так как в этом случае не происходит перегрева сердцевины. При температуре 800°С получается тонкий науглероженный слой, но без следов перегрева, что дает возможность проводить непосредственную закалку в науглероживающую среду. Средняя скорость науглероживания при температуре 1000° по мере увеличения времени выдержки уменьшается и составляет, соответственно, при 3 мин — 0,28 мм, 5 мин—0,42 мм; 7 мин — 0,5 мм
10 мин—0,55 мм. 15 мин—0,65 мм и при 20 мин — 0,67 мм.
Закалка изделий после высокочастотной цементации в жидкой среде осуществлялась тремя методами:
непосредственно после цементации в науглероживающей среде (метиловый спирт);
с повторным индукционным нагревом до температуры закалки (800°) и охлаждением в науглероживающую среду (метиловый спирт);
с повторным индукционным нагреванием образца на воздухе с охлаждением водой в спрейере.
В последнем случае получена твердость 60—62 HRC, в то время как при закалке в метиловом спирте всего 52—55 HRC, что связано с меньшей охлаждающей способностью метилового спирта по сравнению с водой. В структуре стали, охлажденной в метиловом спирте, наблюдается большое количество игл. При их непосредственной закалке с температуры выше 900° получаются перегретые структуры.
Науглероживание в жидких средах имеет большие преимущества по сравнению с другими методами. При этом отпадает необходимость в газовых магистралях, специальных генераторах для приготовления цементующей атмосферы и герметичных реторт. Кроме того, отпадает необходимость защиты мест от науглероживания при местной цементации.
Недостатками этого метода считаются необходимость энергичного охлаждения цементирующей жидкости, непроизводительные потери на ее нагрев, а также трудности, связанные с точным контролем температуры нагрева металла.
Проведены дальнейшие работы по выяснению влияния высокочастотного нагрева на цементацию в спиртах*. Опыты по нагреву трубки диаметром 6/4 и длиной 100 мм, заполненной метиловым спиртом, показали, что при нагреве в соляной ванне при температуре 1000°С выделяется ιμηογο сажи на ее внутренней поверхности (до 1 мм), что замедляет процесс цементации. За 25 мин глубина цементированного слоя составила ОД5—0,4 мм. При нагреве участка 6—7 мм газовой горелкой сажа выделяется тонким слоем. За 10 мин при 900, 950 и 1000°С на углеродистой стали получены слои цементации глубиной, соответственно, 0,25; 0,4; 0,5 мм с резкой границей от основного металла.
Аналогичные данные при обработке в других органических средах получены при использовании токов промышленной частоты и постоянного тока. Образцы из стали 10 диаметром 2 и длиной 60 мм, помещенные в жидкую среду, нагревались пропусканием через них электрического тока промышленной частоты силой 60— 90 а или постоянным током. Образующаяся при нагревании паровая рубашка была неустойчивой, в связи с чем температура по ^лине образца распределялась неравномерно. Стабилизировать паровую рубашку и добиться равномерности нагрева рабочей части образца удалось, помещая их в кварцевые трубки.