Калибрование фасонных профилей
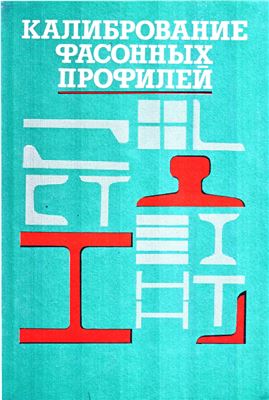
Аргунов В.Н., Ерманок М.З. и др.
Металлургия, 1989 г.
2.2. Волочильный инструмент
Наиболее широкое применение при волочении фасонных профилей сложной формы находят волоки из металлокерамических твердых сплавов. Их отличает износо- и адгезионная стойкость, невысокий коэффициент трения, термостойкость. Эти качества позволяют использовать твердые сплавы для волок, имеющих высоконагруженные зоны (выступы, тонкостенные элементы, переходы между расположенными под углом элементами профиля) при волочении высокопрочных материалов в холодном состоянии и с нагревом. Если вопросы, связанные с выбором материала, изготовлением и эксплуатацией твердосплавных волок для волочения круглых профилей, достаточно широко освещены в литературе [9], то опыт применения твердых сплавов при волочении профилей сложной формы — недостаточно.
Особые сложности возникают при волочении из титановых сплавов и высокопрочных сталей тонкостенных профилей с большим диаметром описанной окружности (до 80 мм) и развитым периметром сечения. Для волочения таких профилей требуются разъемные волоки, работающие в условиях, отличных от тех, в которых эксплуатируются неразъемные твердосплавные волоки, запрессованные в обоймы.
Эффективное применение твердосплавных волок предполагает прежде всего рациональный выбор материала. Используемые в волочильном производстве твердые сплавы состоят из монокарбидов вольфрама (WC) или титана (TiС) и металлического кобальта. Микроструктура сплавов WC—Со является практически двухфазной, состоящей из кристаллитов карбида вольфрама и участков цементирующей фазы. Цементирующая фаза состоит из кобальта, в котором растворено небольшое количество вольфрама и углерода (до 1 %). С изменением соотношения содержания карбидов вольфрама и кобальта изменяются физико- механические свойства сплавов. Важным фактором является также размер карбидных зерен.
В табл. 12 приведены состав, свойства и условия применения в волочильном производстве твердых сплавов систем WC—Со и WC— TiC-Co. Поскольку в процессе эксплуатации волоки для обработки сложных профилей чаще выходят из строя из-за раскалывания под действием ударных нагрузок и поломок при наличии изгибающих усилий, оправданным является использование сплавов ВК15 и В К 20, так как при этом в несколько раз уменьшается число поломок фасонных волок. Эти сплавы, как показал опыт ряда заводов, рационально применять при волочении профилей с диаметром описанной окружности более 35 мм; для профилей с диаметром описанной окружности до 10 мм - сплав ВК6, диаметром 10-35 мм — сплав ВК8.
В общем виде область применения волок из твердых сплавов ограничивают значениями двух факторов: величиной критического давления до прилипания Рп кр и величиной критического давления до разрушения Рр кр. Добиваясь увеличения допустимой величины критического давления до прилипания Рп кр, удается применять твердосплавные волоки вместо алмазных для более тонких сечений протягиваемого металла.
Это может быть достигнуто за счет применения новых смазок, совершенных способов подготовки поверхности, а также путем изменения технологии волочения (частные обжатия, температура, применение специальных приемов, например, гидродинамического подвода смазки, наложения ультразвуковых колебаний). С повышением значения критического давления до разрушения Рр.кр можно увеличить размеры сечений металла, протягиваемого через твердосплавные волоки. Наряду с отмеченными приемами снижения нагруженности инструмента одним из важнейших факторов становится конструкция волоки и способ ее крепления в обойме.
При определенных условиях обработки, например, при увеличении скорости волочения представляют значительный интерес волоки из титано-вольфрамокобальтовых твердых металлокерамических сплавов (WC—TiC—Со). Титаново-вольфрамокобальтовые сплавы с повышением температуры эксплуатации обладают повышенной ударной вязкостью по сравнению с вольфрамокобальтовыми сплавами и сохраняют ее при высоких температурах.
С введением в сплав карбида титана уменьшается налипание твердых сплавов на поверхность стали, а также коэффициент трения при соприкосновении со сталью, отчего повышается стойкость при истирании. Это делает целесообразным опробование титано-вольфрамокобальтовых сплавов, например, Т5К10, Т15К6 при волочении с нагревом профилей из высокопрочных материалов.
Для изготовления волок из твердых сплавов применяют три вида заготовок: стандартные заготовки по ГОСТ3382-74 и ГОСТ 9453-60; отпрессованные в пресс-формы и затем спеченные заготовки; пластифицированные прессованные заготовки. Применение стандартных заготовок волок оправдано для профилей несложной конфигурации, когда
потери твердого сплава при обработке на электроэрозионных станках не превышают 25 % от массы заготовки. При изготовлении волок для профилей чаще не представляется возможным подобрать стандартные заготовки требуемых размеров. В этом случае для профилей простых форм (круг, квадрат, шестигранник) заготовки получают прессованием с последующим спеканием. После спекания волоки подвергают только окончательной доводке для удаления дефектного слоя, достижения требуемых точности карала волоки и шероховатости поверхности. При такой технологии изготовления волок необходимы специальные пресс-формы для каждого типоразмера волок.
Сам процесс изготовления пресс-форм является весьма трудоемким. Для точной подгонки деталей фасонной пресс-формы требуется применение квалифицированного ручного труда до 30 нормочасов. Поэтому экономически целесообразно изготавливать волоки по схеме прессование — спекание при годовой потребности каждого типоразмера не менее 20 шт. Расчет размеров пресс-форм производят с учетом коэффициента усадки в процессе спекания, припуска на удаление дефектного поверхностного слоя и припуска на устранение искажения формы заготовки в процессе спекания.
Коэффициент усадки R принимают в зависимости от марки спекаемых сплавов следующим: ВКЗ, ВК8 1,20; ВК15 1,23; ВК20 1,25. Необходимо учитывать, что коэффициент усадки может изменяться в зависимости от дисперсности порошков в пределах 1-2 %. Прессование осуществляют на механических или гидравлических прессах, обеспечивая величину средних рабочих напряжении на рабочей поверхности пуансона 30-40 МПа.
В условиях мелкосерийного и единичного производства наиболее приемлем разработанный во ВНИИТС способ получения пластифицированных заготовок. Сущность метода заключается в прессовании порошка с пластификатором, который представляет собой раствор каучука в бензине. Затем заготовку спекают при 650-700 °С в среде водорода. Спеченные заготовки пропитывают парафином. Такая заготовка хорошо поддается последующей механической обработке. При спекании пластифицированной заготовки вследствие более однородной плотности порошка по объему, чем при прессовании в пресс-форме искажения формы уменьшаются, а потому и допуск уменьшается. Благодаря указанным преимуществам пластифицированные заготовки применяют при изготовлении в условиях единичного производства твердосплавных волок для волочения в нагретом состоянии широкого сортамента тонкостенных профилей из высокопрочных сталей и титановых сплавов.
Корнеев Н.И., Хабаров Н.Д., Тарасов В.И. предложили выполнять составную волоку с наружной поверхностью в виде конуса с самого рмозя щи мся углом. По их мнению, части такой волоки, наложенные на профиль, будут затягиваться до окончательного размера под действием усилия волочения. Как показал последующий анализ предложенного способа и проведенные эксперименты, выполнение наружной поверхности составной волоки в виде конуса является условием необходимым, но недостаточным для обеспечения процесса затягивания частей волоки. В связи с этим возникла необходимость в создании специального устройства, обеспечивающего волочение тонкостенных профилей без острения захваток. На основе этого принципа было создано оригинальное устройство, ранее не применявшееся в промышленности (см. рис. 9).
В зависимости от конфигурации профиля применяют разъемные волоки, состоящие из двух, трех или четырех частей. Твердосплавный вкладыш составной волоки (рис. 12) крепится в разъемном корпусе, который выполняется из инструментальной стали У10. К стальным деталям корпуса вкладыш припаивают самофлюсующимся припоем ВПр4 или латунью Л62. Пайка производится на высокочастотной установке. Детали корпуса волоки с укрепленными твердосплавными вкладышами и уложенной в зазоры между ними фольгой припоя помещают в кварцевую трубку, продуваемую аргоном, нагревают выше температуры плавления припоя на 100-150 °С (до 1050- 1100°С), выдерживают при этой температуре в течение 3—5 мин и охлаждают при продувке аргоном до 300—350°С, а затем на воздухе. После пайки производят окончательную доводку размеров волок в сборе.