Дисперсионное упрочнение стали
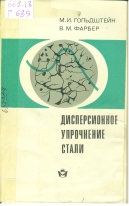
Гольдштейн М.И., Фарбер В.М.
Металлургия, 1979 г.
ДИСПЕРСИОННОЕ УПРОЧНЕНИЕ И СКЛОННОСТЬ СТАЛИ К ХРУПКИМ РАЗРУШЕНИЯМ
Склонность к хрупким разрушениям дисперсионноупроч ненной стали является важнейшей характеристикой конструктивной прочности изделий наряду с пределом текучести стали. Повышение прочности сталей обычно приводит к снижению вязкости, уменьшению работы развития трещины, повышению порога хладноломкости, т. е. увеличению склонности к хрупким разрушениям. По данным работ [206, 239], увеличение предела текучести низколегированных строительных сталей на каждые 1,5 кгс/мм2 вызывает повышение порога хладноломкости на 4°.
Дисперсные частицы могут приводить к увеличению склонности к хрупким разрушениям не только вследствие собственно упрочнения, но и вследствие образования выделений по границам зерен и блокирования ими дислокаций. Положительное влияние дисперсных частиц на уменьшение склонности к хрупким разрушениям может проявляться лишь в случае, когда дисперсные частицы способствуют измельчению зерна.
Выделения по границам зерен (см. рис. 26, а) не вносят сколь-либо заметного вклада в упрочнение по сравнений с выделениями внутри зерна. В то же время крупные пограничные частицы могут являться центрами зарождения трещин и будут уменьшать прочность сцепления отдельных зерен. Такие выделения на границах иногда приводят к образованию «мягкой» свободной от частиц зоны вблизи границ, что также способствует меж- зеренному разрушению. Отрицательное влияние оказывают различные строчечные выделения не только по границам, но и внутри зерна (см. рис. 26,в).
С этой точки зрения, состав сталей и технология их обработки должны обеспечивать минимальное количество выделений по границам зерен и наиболее их равномерное распределение внутри зерна. Это подтверждается экспериментальными данными на стали 20Г2Ф.
Сталь 20Г2Ф подвергали обработке по трем режимам:
- Нагрев 1100° С, закалка в воде, отпуск при 200° С. Упрочняющая фаза — карбид ванадия — в этом случае была полностью растворена в аустените; в стали не было дисперсных упрочняющих частиц. При 20° С процент волокна в изломе составлял 45, Гхл=—30° С.
- Нагрев 1100° С — переохлаждение на 800° С — выдержка 3 мин, охлаждение в воде, отпуск 200° С. В этом случае при изотермической выдержке при 800° С, 3 мин, в соответствии с ранее приведенными данными (см. гл. IV), в аустените выделяются крупные частицы карбида ванадия, располагающиеся в виде строчек по границам зерен. Процент волокна в изломе равен 40, Тхл——10° С.
3. Нагрев 1100° С — переохлаждение на 800° С — выдержка 2 ч, охлаждение в воде, отпуск 200° С. Эта обработка отличается от предыдущей обработки только значительно большим временем выдержки при 800° С, вследствие чего образовавшиеся по границам карбиды ванадия были более крупными и их было больше. Перлитного превращения в процессе переохлаждения не происходило. В этом случае излом был полностью кристаллическим, а Tхл=0°С.
В результате при всех указанных видах обработки образцы, хотя и имели одинаковую твердость, однако их склонность к хрупкому разрушению была различной.
В том случае, когда образовывались строчечные выделения карбида ванадия, особенно по границам зерен, происходило уменьшение доли волокнистой составляющей в изломе (характеризующей работу развития трещины) и повышение порога хладноломкости.
Из изложенного вытекает, что в практических условиях охлаждение малоуглеродистых сталей с целью уменьшения склонности к хрупким разрушениям должно проводиться как можно быстрее до начала перлитного распада. Во всяком случае, следует избегать замедленного охлаждения в интервале температур 900— 700° С. С этих же позиций можно считать, что одной из причин лучшей хладостойкости низкоуглеродистых сталей, упрочненных нитридами, по-видимому, является то, что нитриды ванадия выделяются по границам аустенитных зерен в значительно меньшей степени, чем карбиды ванадия. Это связано с тем, что скорость процесса выделения нитридов из аустенита при 800° С, согласно данным работы [234], значительно меньше, чем карбидов.
Блокирование или закрепление дислокаций дисперсными частицами уменьшает работу пластической деформации, приводит к росту локальных «пиковых» напряжений, уменьшению возможности их релаксации и, как следствие этого, к увеличению склонности к хладноломкости. Следовательно, выделения по границам зерен и закрепление дислокаций выделениями, как факторы, сопровождающие дисперсионное упрочнение, будут отрицательно сказываться на хладноломкости стали и повышать склонность стали к хрупким разрушениям. Поэтому следует еще раз подчеркнуть, что собственно дисперсионное упрочнение всегда приводит к повышению склонности сталей и сплавов к хрупкому разрушению. Лишь косвенные факторы, сопровождающие дисперсионное упрочнение, могут в какой-то степени компенсировать вредное влияние собственно дисперсионного упрочнения на хладноломкость металлов. Таким косвенным фактором, почти всегда сопутствующим дисперсионному упрочнению, является измельчение зерна. Как отмечалось выше, измельчение зерна стали в дисперсионно упрочненных материалах происходит вследствие торможения роста зерна дисперсными частицами при нагреве, благодаря влиянию дисперсных частиц на зарождение кристаллов новой фазы при фазовом превращении и т. д.
Уровень предела текучести стали типа 09Г2 повышается при наличии в ней карбидов ванадия (сталь 09Г2Ф) и особенно комплексной карбонитридной фазы ванадия и ниобия (сталь 09Г2ФБ). Несмотря на заметное упрочнение сталей при легировании ванадием и ниобием, температура перехода их не увеличивается. Вредное влияние упрочнения на хладостойкость компенсируется измельчением зерна (сталь 09Г2Ф). Более того, в стали 16Г2АФ, упрочненной карбонитридами ванадия, в результате наиболее сильного измельчения зерна достигается одновременное повышение предела текучести и снижение температуры перехода. Так, у стали 16Г2АФ, упрочненной нитридами ванадия, размер зерна обычно соответствует номеру 9—10, тогда как у аналогичной стали 14Г2, но без нитридной фазы — номеру 5—6. Такое изменение размера зерна, в соответствии с вышеприведенными данными, может привести к снижению порога хладноломкости на 40—80° С. Однако в обратную сторону влияет дисперсионное упрочнение, за счет кото- рого предел текучести стали 16Г2АФ на 10—12 кгс/мм2 выше, чем стали 14Г2. Такой прирост прочности дает повышение порога хладноломкости примерно на 30° С. Учитывая совместное, но противоположное влияние собственно дисперсионного упрочнения и величины зерна, получаем, что в целом порог хладноломкости стали 16Г2АФ благодаря нитридному упрочнению должен быть даже ниже, чем у стали 14Г2.
Таким образом, в сталях с карбонитридным упрочнением в сильной степени проявляется косвенный механизм дисперсионного упрочнения — зернограничное упрочнение вследствие измельчения зерна.
В свете изложенного, оптимальное легирование и термическая обработка дисперсноупрочненных сталей должны обеспечивать получение не только прироста прочностных свойств, но и сохранение на необходимом уровне пластических и вязких свойств, т. е. сочетание упрочненного состояния с малой склонностью к хрупким разрушениям. Это достигается при правильном легировании и обработке сталей в соответствии с отмеченными выше закономерностями. Так, содержание легирующего элемента, определяющего эффект дисперсионного упрочнения, в большинстве случаев должно быть таким, чтобы максимум вторичной твердости не наблюдался. Это достигается в низкоуглеродистых феррито-перлитных сталях, применяемых в горячекатаном или нормализованном состоянии, при легировании до 0,1% V (стали 15ГФ 15Г2СФ, 18Ф и т.п.), до 0,05% Nb (10Г2Б), а в арматурной стали до 0,14% Zr (20ХГ2Ц). В сталях подобного назначения, но с нитридным упрочнением достигаются значительно лучшие механические свойства при содержании азота 0,015-0,025% и ванадия 0,08-0,15% (15Г2АФ, 16Г2АСФ и т.п.). При больших содержаниях указанных элементов происходит дальнейшее увеличение прочности, но ухудшается хладостойкость. Легирование подобных сталей титаном даже в очень малых количествах (до 0,05%) неэффективно, поскольку регулирование дисперсности его карбидов и нитридов в процессе прокатки или термической обработки практически невозможно. Эффективным является совместное легирование несколькими элементами, например: 0,08% V +0,03% Nb; 0,08% V+0,03% Nb+0,02% Ti; в сталях с азотом 0,10% V+0,03% А1 и т. п.
В среднеуглеродистых улучшаемых машиностроительных сталях использование эффекта дисперсионного упрочнения дает хорошие результаты также при небольшом содержании таких упрочнителей, как ванадий (до 0,1—0,15%) и ниобий. Однако содержание менее эффективных в отношении дисперсионного упрочнения элементов, таких как хром, молибден, вольфрам и др., может быть значительно большим и определяется необходимостью обеспечения таких свойств, как прокаливаемость, малая склонность к обратимой отпускной хрупкости и т. д. В подобных сталях (40Ф, 40ХФ, 30Χ3ΜΦ и т. п.) наилучшие свойства достигаются после закалки и высокого отпуска, обеспечивающего образование полностью некогерентных с матрицей дисперсных частиц, т. е. отпуск должен проводиться на более высокую температуру, чем та, когда достигается максимальное упрочнение. Однако в ряде сталей используется обработка вблизи «пика» вторичной твердости. Так, нашедшие в последнее время широкое применение высокопрочные 5%-ные хромистые стали содержат около 1% молибдена и 0,5—1,0% ванадия (40Х5МФ). Наилучшие свойства достигаются после закалки и высокого отпуска (~600°С) несколько выше пика вторичной твердости.
В жаропрочных аустенитных сталях с карбидным [37Х12Н8Г8МФБ (ЭИ481)] или сплавах с интерметал- лидным упрочнением [ХН35ВТР (ЭИ612)]; [ХН77ТЮР (ЭИ437Б)] пересыщенный при закалке аустенит подвергается старению при температуре вблизи максимума дисперсионного твердения. Аналогично на максимум дисперсионного твердения обрабатываются мартенситно- стареющие стали. Таким образом, собственно дисперсионное упрочнение увеличивает склонность стали к хрупким разрушениям за счет увеличения прочности, образования относительно крупных выделений по границам зерен, закрепления дислокаций выделениями.
Уменьшение размера зерна благодаря дисперсным частицам является единственным и существенным фактором, позволяющим компенсировать вредное влияние собственно дисперсионного упрочнения на сопротивление стали хрупким разрушениям. При существенном уменьшении размера зерна отрицательное влияние дисперсионного упрочнения может быть не только скомпенсировано, но и достигнуто одновременное повышение прочности и снижение порога хладноломкости.