Кристаллический излом
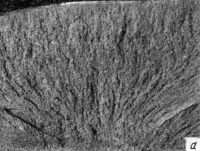
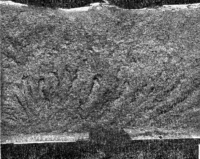
Характеристика.
Представляет собой однородную поверхность хрупкого разрушения с кристаллическим строением без заметных признаков макропластической деформации. Образуется при температурах испытания ниже критической температуры хрупкости (КТХ100). Характерен для литых и деформированных сталей.
Поверхность разрушения, как правило, светло-серая. Кристаллический излом возникает при разрушении по границам зерен (такой излом иногда называют зернистым) или по кристаллографическим плоскостям, проходящим по телу зерен, что обусловливает значительную отражательную способность излома, придавая ему характерный металлический блеск.
Утяжки на боковых сторонах изломов либо отсутствуют, либо имеют очень малую величину, что свидетельствует о незначительной пластической деформации металла при его разрушении. При больших увеличениях, на поверхностиразрушения выявляются фасетки скола, квазискола или межзеренного разрушения.
Условияобразования хрупкого кристаллического излома (факторы, влияющие на повышение КТХ):
1.При выплавке стали —
а)применение шихты, загрязненной вредными примесями (см. Волокнистый излом);
б)неправильная последовательность легирования, раскисления и модифицирования стали;
в)неправильный выбор геометрии изложницы и условий теплоотвода, низкая скорость кристаллизации и последующего охлаждения слитков, что ведет к повышенной химической неоднородности литой стали, повышенному содержанию и неравномерному распределению неметаллических включений;
г)повышенное содержание газов в стали.
2.При горячей деформации —
высокая температура ее конца и медленное охлаждение в области температур до начала фазовых превращений.
3.При термической обработке —
а)перегрев металла перед закалкой, но не выше критической температуры образования нафталинистого или камневидного излома;
б)охлаждение при закалке со скоростью ниже критической, что приводит к появлению в структуре большого количества немартенситных продуктов превращения аустенита (в случаях а и б разрушение смешанное — по границам бывших аустенитных зерен и по телу зерен);
в)отпуск в зоне температур обратимой и необратимой отпускной хрупкости (вызывает разрушение преимущественно по границам бывших аустенитных зерен);
г)недостаточные продолжительность или температура высокого отпуска, при которых не достигается необходимая коагуляция карбидов, что снижает вязкость и пластичность стали (разрушение смешанное — по границам и по телу зерен);
д)недостаточная скорость охлаждения после высокого отпуска, вследствие чего развивается обратимая отпускная хрупкость (разрушение преимущественно по границам бывшего аустенитного зерна).
Дляпредупреждения возникновения кристаллического излома необходимо:
—применение чистой шихты;
—тщательное раскисление и удаление шлака и оксидов из жидкой стали;
—повышение скорости затвердевания и охлаждения металла;
—применение нагрева перед закалкой в интервалетемпературАс3+ (30-100) °С;
—обеспечение при закалке скорости охлаждения не ниже критической.
—проведение отпуска при температуре, предотвращающей развитие обратимой и необратимой отпускной хрупкости;
—применение ускоренного охлаждения после отпуска;
—длительность отпуска, достаточная для коагуляциикарбидных выделений.
Сталь, кристаллический излом которой обусловлен неправильно проведенной термической обработкой, может быть исправлена:
—если уровень прочностных свойств превышает заданный — путем повторного отпуска или отпуска при более высокой температуре, чем ранее проведенный;
—если уровень прочностных свойств ниже заданного — путем повторной закалки и отпуска по откорректированным температурно-временным режимам.
Механическиесвойства.
Сталь, имеющая кристаллический излом при температуре эксплуатации, характеризуется пониженной ударной вязкостью по сравнению с той же сталью, имеющей волокнистый излом. При этом, чем крупнее величина зерна в изломе, тем более хрупкий характер разрушения стали.
Источник: Атлас дефектов стали. Пер. с нем. М. "Металлургия", 1979.